Rolling non-inventoried costs into assembled goods.
If you need to add a non-inventoried cost to an assembly, whether it be shipping cost, labor cost, waste fees or any other kind of costs, check out this article.
- Create a non-inventoried, other charge, shipping, or labor product in Acctivate and name it to correspond with the kind of cost you'd like to add, such as "Labor" or "Shipping."
- Set the cost method to Standard. Standard cost allows you to assign an internal cost per warehouse to your non-inventoried items. A full explanation of standard cost for this purpose can be found here.
- Set the cost for each warehouse and the Unit of Measure as desired.
- Open the parent item of the assembly and add the newly created item as a component on the assembly and set the quantity. If the qty isn't fixed I.E. a labor charge where the number of hours or "units" may change mark the component as "variable." Please note: In order to be able to set components as variable, the assembly must be a custom or process assembly. You can change assembly type by changing the "Bill of Materials" on the product window.
- Ensure that you have a "Non-inventory offset account" set for the warehouses that you will be building assemblies into otherwise a "Transaction not in balance" sync error will appear on your next QuickBooks sync. The offset account should be an account that will track the cost, so something like a "Labor" account or "Shipping fee" account.
- Ensure that you have a "Non-inventory offset account" set for the warehouses that you will be building assemblies into otherwise a "Transaction not in balance" sync error will appear on your next QuickBooks sync. The offset account should be an account that will track the cost, so something like a "Labor" account or "Shipping fee" account.
- If the component was marked variable, you can delete the cost or adjust the quantity under the "Unit Qty" column for the item in the assembly session window before posting.
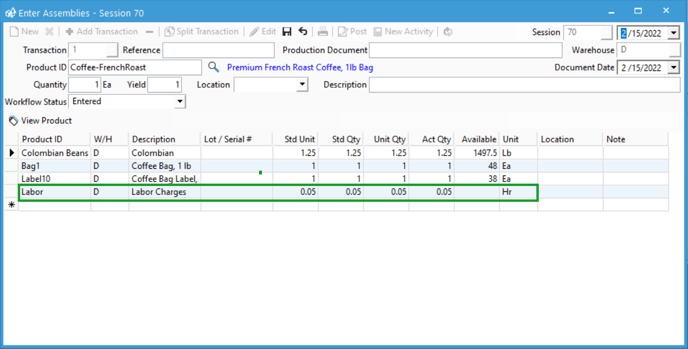
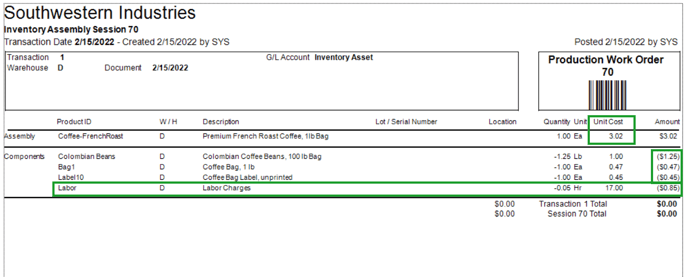