Using Sales Order Manager to allocate inventory when scheduling.
This article explains the use of Order Manager for inventory allocation.
In Acctivate, inventory will not be allocated to booked or back-ordered orders automatically. Those orders need to have inventory scheduled manually, even if there is now a sufficient quantity in your warehouse(s). Of course, it's not always practical to manage orders one at a time if you have a lot to work with. Order Manager let's you manipulate or update orders in batches. A common use would be using the Schedule action on orders that need to have inventory available scheduled to them. Since this is done in batches, what happens if you don't have enough inventory to fill all the orders? Are some prioritized over others?
The Order Manager actually works in sequence with the list of orders as it currently shows in the Order Manager window. It allocates inventory from the top-most selected order to the bottom. There is no priority for order date, requested date, customer ID, or any other factor unless you sort the order list to in such a way. This can be quite helpful if you have more ordered than available and you want to allocate inventory to those orders with a specific priority in mind. You could sort by any of the values in Order Manager. If sorting doesn't give you the order of priority you need, you can always select groups of orders and update in smaller batches.
Here's an example:
Let's say you have two back-ordered orders. One of them has Button with a quantity of 5 as a line item. The other, created after the last order, also has Button but with a quantity of 2. You have been waiting on your vendor to ship the product and have just received a quantity of 5 for Button. Since your total requirement for the product in your unscheduled orders is 7, you won't have enough to complete both.
If you sort the Order Manager list by 'Order Date', the oldest sales order will appear first. Using the Schedule action with the two orders selected will attempt to schedule them both, starting with the first. The order for 5 Buttons will be fully scheduled and since there aren't any left in the warehouse, the order for 2 Buttons will remain back-ordered.
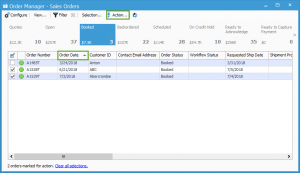
If you click 'Order Date' again, it will be sorted with the youngest date at the top. Using the Schedule action with this sorting would schedule the entire order for 2 Buttons. The order for 5 Buttons however would only have 3 scheduled leaving the other 2 to still be back-ordered.
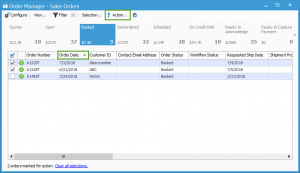