Selling a product in multiple package sizes.
Acctivate has multiple options for selling multiple sizes of the same product, such as a single unit (each), a pair, pack and/or case. Using the Kit function in Acctivate, we can easily accomplish this task.
Units of Measure
First, you may want to consider Configuring Multiple Units of Measure to stock the item in one unit, but have alternate units for purchasing and sales. However, this approach uses the same Product ID (SKU), UPC, Description and other attributes.
Kits
You may need to have a different Product ID or UPC per each unit of measure. If so, the Kitting add-on module is a great way to create a special Product ID that can be used to automatically sell a fixed number of items.
For example, you may stock and typically sell individual calendars. However, you have a ten-pack bundle and you'd like a separate product ID, UPC and Description.
You would create a new Kit product containing 10 calendars (Components tab). Each unit sold of the Kit product would pull 10 calendars from inventory.
Kit Considerations
Your customers can place orders using the Kit product ID and you won't have to verify the desired unit. Proper pricing will always be selected, which simplifies order entry. This ultimately reduces costly mistakes like selling a case for the each price.
Kits are Non-Inventoried items containing Inventoried Components. The components will be removed from inventory automatically when the Sales Invoice is created for the Kit. On the other hand, a Credit Memo with a Kit item will return the Inventoried Components back to your warehouse rather than the Kit itself. Unlike Inventoried Assemblies, Kits do not need to be "built" using a separate inventory transaction.
You will need to maintain multiple product IDs in Acctivate for the same product, for each packaging. Requirements, such as a different Product ID and Description, may eliminate this concern. Using the Import Data (Products) tool to import a list from Excel should reduce the time to set up the kit items.
Kits must be picked from a single warehouse. The warehouse for all components is selected from the Warehouse on the main Sales Order line. This shouldn't be a concern with the above scenario, but Inventory Assemblies may need to be used if you're looking for a kit pulling components from different warehouses.
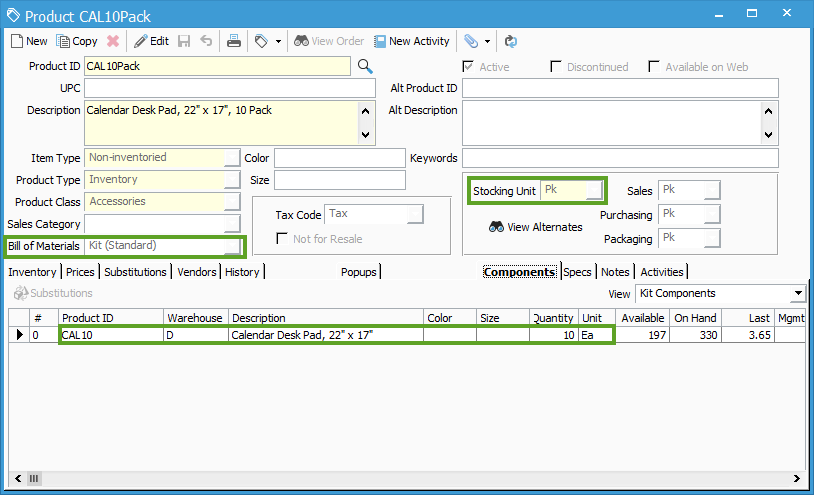