What are the Bill of Materials Options for Manufacturing?
Acctivate supports a variety of Manufacturing options, including Build-to-Order and Build-for-Stock Manufacturing. Kits, Assortments, Custom and Process Assemblies are add-on modules.
Acctivate supports a variety of Manufacturing options, including both Build-to-Order and Build-for-Stock Manufacturing. A single Bill of Materials type must be selected for each manufactured product in Acctivate. The following Bill of Materials choices are available. Acctivate uses the term Assembly for build-for-stock and Kit for build-to-order.
Note: Kits, Assortments, Custom and Process Assemblies are add-on modules, Please contact the Acctivate Sales Team for more information.
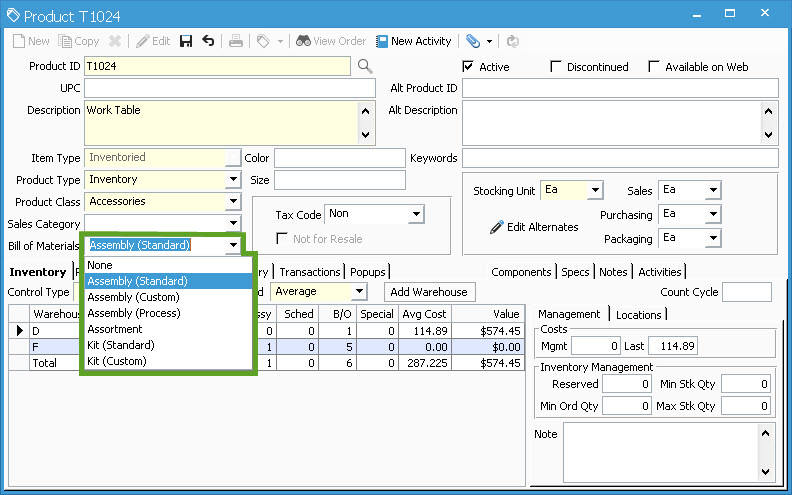
Assembly (Standard)
Acctivate includes manufacturing functionality in the base system with the Standard Inventory Assembly function. This includes the ability to create finished goods inventory for an item from one or more components from raw materials inventory. The raw materials (components) are allocated to Work in Process inventory during production, restricting them from other assemblies and/or sales orders.
Component inventory may be selected from multiple warehouses, Workflow Status can be tracked and multiple items/transactions can be managed under a single batch Session.
Assembly (Custom)Custom Assemblies include all of the Standard Assembly functionality, along with the ability to modify the component list for each assembly transaction. Acctivate allows you to Add, Remove and/or Update Quantities for components of a Custom Assembly.
Assembly (Process)Acctivate supports Process Manufacturing, primarily for the Food, Beverage and Medical industries. Process Assemblies allow you to manage a variable bill of materials, similar to Custom Assemblies.
Process Assemblies also allow you to track the original Production Quantity, the actual Yield Quantity and the Variance. This is an important metric for any manufacturer looking to reduce costs through better management.
Kit (Standard)Standard Kits are similar to Standard Assemblies, but they are build-to-order. This allows you to maintain the component inventory only and an additional inventory transaction to “build” the kit is NOT necessary.
Standard Kits require a fixed bill of materials (component) list. Component inventory must be selected from a single warehouse, selected on the Sales Order line.
Kit (Custom)Custom Kits are similar to Standard Kits with some additional functionality. You can Add and Remove components and adjust the Component Quantities for a single Sales Order.
Custom Kits also support the ability to Substitute components if the standard component item is either unavailable or not desired for a sales order.
AssortmentThe last Bill of Materials type is not generally considered “manufacturing”. Instead, an Assortment is a way of taking orders for a single item (e.g., style) and selecting multiple items for sizes, colors and/or variations that do not adjust the price. We’ve found that assortments are typically used in the garment and accessories industries.